The Sabanto Autonomy System is a retrofit kit and software system that transforms tractors of multiple brands and sizes into autonomous vehicles that can operate a variety of agricultural implements to perform work day or night, without continuous oversight.
What is the most striking detail?
Your autonomous tractor is already sitting in your machine shed. After a one-day installation process, farmers can use their existing tractors to perform a variety of field operations autonomously. Our advanced but easy to use technology gives users the capability to remotely control and monitor tractors with a cell phone from any location. Farmers can still operate their equipment manually with the flip of a switch.
How does the robot tractor with your autonomous retrofit kit navigate and plan its work and paths?
The field boundary, plus any internal objects to be avoided, is recorded one time while manually driving the tractor. Afterward, our cloud-based software creates a path plan for the recorded field geometry using a designated pass angle, pass overlap and number of headland passes.
The generated path plan is downloaded to the main processing unit on the tractor. Once field conditions are verified via onboard cameras, the operator remotely initiates the system and the tractor begins to follow the generated path. The system continually monitors its own performance and detects any anomalies, which can be viewed in real-time by the operator using our mission control software on a phone or laptop. If the system requires any attention, the operator is sent an SMS/text message to their phone. Otherwise, the tractor continues to run until the path plan is completed and then transits to a desired field destination or onto the next field.
Throughout the entire field operation, vehicle and autonomy data are gathered and streamed back to our cloud software, where it can be monitored by the grower and if needed, by our support team.
Are implements operated and controlled by the robot tractor with your autonomous kit?
A tractor’s 3-point hitch position, remote valves and PTO shaft operation are controlled by our system.
Because of our relationships with implement manufacturers, we monitor the performance and status of an attached implement via an interface with sensors installed on the implement to detect anomalies.
What safety features do you offer?
Our safety system detects obstacles and closely monitors the health of the tractor and the implement using 360-degree cameras that capture photos and stream video on demand.
What is the cost price per ha compared with a manned tractor?
Our cost to perform a field operation is considerably less than the status quo used in row-crop agriculture across the US.
What kind of work can your system do autonomously?
Our customers use their Sabanto Autonomy System for mowing, seeding, tillage, rolling, rototilling, discing and cultivating. We have also demonstrated capabilities planting and spraying.
Can you switch off autonomous mode and continue as a manned tractor for difficult work/circumstances?
An operator can transition from autonomous mode to manual mode with the simple flip of a switch, allowing a tractor to be used as it was originally intended.
How many systems are currently in the field and where?
Sabanto was founded in October 2018.
How many units do you currently have in the field and where?
We have many units situated across the US, as well as Canada, on Kubota, Fendt and John Deere tractors. We have hundreds of units running in the US from California to New York and Texas to Wisconsin. We also have systems running in Canada.

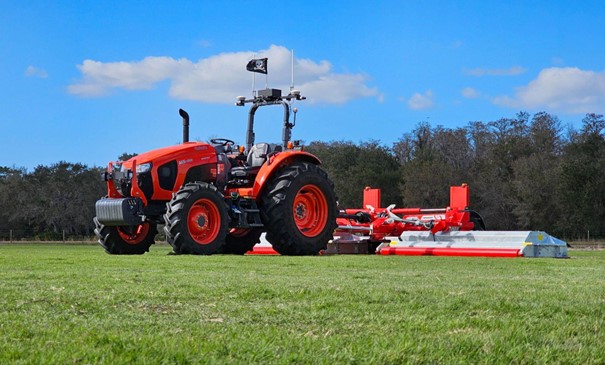

Specifications
Company name and nationality | Sabanto, Inc. USA |
Product name | Sabanto Autonomy System |
Suitable brands and tractor/vehicle models | John Deere 5E series (cab and open station) 5075E 5085E 5090E 5100E 5M series (cab and open station) 5090M 5095M 5100M 5105M 5115M 5120M 5130M 6E series (cab) 6105E 6120E 6135E Kubota M5 series (cab and open station) M5-091 Fendt 700 Vario (cab) Gen 6 |
Technical requirements for tractor/vehicle | Electronic shuttle, factory grill guard, wheeled – not tracked |
Is your solution Isobus compatible? | No |
Possible minimum and maximum driving speeds | 11.3 km/h 1.6 km/h 7.0 mph 1.0 mph |
Main components autonomous retrofit kit | Proprietary main control unit CAN bus monitoring interface Satellite corrected GNSS receiver High gain cellular communication antennas Sensors and perception system for forward collision avoidance and situational awareness Depending on the tractor model, we install actuators for braking and three-point hitch control, remote steering and hydraulic valves, and wheel angle sensors |
Operator or driver nearby required | No |
Price (in €/US$) | Contact Sales@Sabantoag.com for pricing information. |
Countries the product is for sale/rent in 2024 | United States, Canada, Australia |